My good friend John owns (among other things) Heartland Permacolumn. I’ve borrowed this from his website (https://www.heartlandpermacolumn.com/products/the-perma-column-price-advantage/):
“Perma-Column products give you the ultimate price advantage. You simply cannot put up a building on a concrete foundation for less money.
Yet some may say, “They’re too expensive…”
HOWEVER, the only people who ever say this install buildings using treated wood posts embedded directly in the soil. They think adding between one and three thousand dollars to a building makes the price “outta sight…”
It is true that there is one type of building that is less expensive than a Perma-Column building…one built on a treated wood foundation. Treated wood posts may last a very long time in soil contact in some cases…and not so long in other cases. This is part of what makes post-frame buildings the most economical of all building types.
But there are several other reasons why post-frame is so economical and efficient. First, it is much quicker, easier and less resource-intensive to stick a post in the ground and build from there than it is to build any other type of building on a typical foundation.
Second, by using posts that are 8′ or more on center, you have far fewer structural members to install compared to other types of buildings.
Third, because the structure is made of wood it is less costly, requires no fancy equipment or specialty trades, is easier to work with, is very environmentally-friendly and is energy-efficient.
Furthermore you can build exceptionally high sidewalls (usually 24′, sometimes more) and exceptionally wide clear-spans (100′ or more without supporting walls or columns) for ultimate design efficiency and flexibiliity. All of these advantages remain firmly in place when you build on concrete piers or a continuous concrete foundation using Perma-Column products.
When one takes a close look at costs per linear foot, the upgrade is not really very much at all. A Perma-Column upgrade is typically between $10 and $11 per linear foot compared to the price of building on treated wood posts embedded directly in the ground. This may increase the price of a really small and inexpensive agricultural building by more than 10%, but it may also add less than 4% to the total cost of a really nice one…or to a typical commercial, residential or industrial building. Click here to download a PDF that provides a cost comparison.
So if you want a REALLY cheap building and don’t care when or if the post foundation will rot, you should build a post-frame building on a treated wood post foundation…
…or for roughly 10% more, you can build using Perma-Columns and have an investment that will hold its value for a very, very long time.”
Mike the Pole Barn Guru writes:
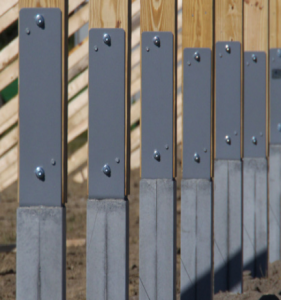
Perma-Column
This particular article has been triggered by a question posed by reader MATT in WABASH who writes:
“What is the cost of a perma-column? I am looking at a 40 x 56 building most likely at a residence that I will live long term and thought perma-columns would be a good investment, but I am having trouble finding the cost online for them. Thanks!”
Well Matt, as near as I can tell, the budget should be around $200 per column by the time they get delivered to your jobsite. Next challenge is going to be unloading and properly placing the several hundred pound Perma-columns exactly in the holes, on top of a poured concrete footing.
With the thought you are trying to avoid placing pressure preservative treated wood into the ground, there may be a more affordable (and easier to install) alternative. Assuming four foot deep two foot diameter holes, one could pour under one-half yard of premix in the hole and mount a bracket in it for roughly $100. Same longevity, same concept, easier to install.