ZIP Sheathing and Other Post Frame Thoughts
Reader SPENCER in WINLOCK writes:
“Hello, I’m in the planning phase and your roof purlin style and watching the “Hart and Home” youtube series have just about convinced me to go with Hansen buildings. I have a few general questions. 1. I have a tight driveway with a gate. What kind of a truck would 40′ trusses be delivered on? 2. I’d like to use zip panels on my walls and roof for sheathing below the metal. Is this something that can be added to the engineering package and supplied by me? I’m assuming the weight of the panels would need to be accounted for in the roof loading. 3. Are 20′ side walls a possibility with your buildings? 4. I’d like to use poured columns and wet set brackets for my footings. Is this something that can be added to the engineering package and supplied by me? My goal would be to have these installed well before taking delivery of the building. 5. I’d like to do a lean-to but need to keep as much roof height as possible for a 14′ door. Do these have to be designed with trusses or can I specify dimensional lumber? Thank you!”
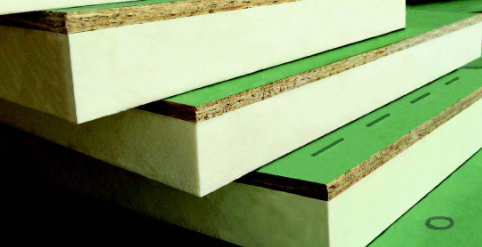
Mike the Pole Barn Guru responds:
For those following along at home – Hart and Homes YouTube series can be viewed here: https://www.youtube.com/channel/UCjzEsuHQ8UFZEbXQc16RT9Q
Hansen Pole Buildings has provided more fully engineered post frame buildings to our clients in Washington State (roughly a 1000 at last count), than any other state. Mr. and Mrs. Hart are a great couple and have been a pleasure to work with. This roof purlin style (purlins on edge) is fairly typical in Western U.S. post frame buildings, however, recessing them between trusses with joist hangers is not. Our feeling is this engineered connection is far superior to attaching purlins to a very small block full of nails (extended reading on paddle blocks can be found here https://www.hansenpolebuildings.com/2012/05/paddle-blocks/).
In answer to your questions:
1) Regardless of supplier, both roof trusses and steel roofing/siding are typically delivered by semi-trucks pulling 48′ trailers. You may want to make provision to have a utility trailer handy for at least a steel package to be off loaded onto, should you feel your entrance is just too tight for this sort of truck/trailer combination.
2) Zip System sheathing was introduced by Huber Engineered Woods in 2008 and it has been widely adopted in many U.S. states. Huber manufactures premium OSB products such as Advantech sheathing. Many builders prefer Advantech over plywood, due in part to quality problems they were seeing in plywood.
Zip System sheathing’s chief virtue is it marries a water-resistant barrier (WRB) to sheathing, eliminating the step of adding a separate WRB. Many builders like the Zip system a lot because it eliminates what has always been a troublesome step in building processes. This is, carefully installing large plastic sheets around an entire building, carefully lapping it at seams, and more carefully cutting and taping around doors and windows so it directs any water to the exterior.
While Tyvek (first popular building wrap), was originally marketed as an energy-saving material, it was soon disproven that a building with Tyvek, installed typically, wasn’t much tighter than a conventional building with asphalt felt.
A building built with Zip sheathing, however, taped and sealed as recommended, produces very tight results without a lot of fussing. This is especially true in relatively simple building plans without a lot of bumps, angles, and complex shapes.
Main Zip Sheathing downside is a heavy reliance on flashing tape. Huber makes high-quality tape in various widths and also makes a stretch version for window pan flashing and other tricky details. Still, water, frost, or dirt can undermine a watertight seal, as can sloppy installation.
Liquid-applied sealants offer an alternative to tape and is gaining in popularity. One example is Huber’s Liquid Flash, a thick liquid flashing applied with a caulking gun and spread with a trowel. Liquid flashing provides a nearly foolproof solution for waterproofing window pans, foundation joints, and other tricky or vulnerable transitions.
Like any product or system Zip sheathing has pros and cons. Some are actual and proven, some more theoretical. This product has not really been around long enough to stand time’s test. But, there are few in field failure reports and most contractors who have tried this system are happy with it overall.
Here are main arguments, pro and con:
Pros
- Installs sheathing and water-resistant barrier in one step. Saves labor.
- Makes it relatively easy to create a very tight shell.
- This is a complete system with high quality tapes and liquid sealant, as well as published details backed by a reputable company.
- Backed by a 30 year warranty, but not transferable, and subject to usual conditions about proper installation.
- Window installation and flashing is easier than with building wrap (but relies on tape at window head flashing). Eliminates Origami style building wrap folding.
- Quick dry-in for contractor with less concern about wind and water.
Cons
- Tape must be installed carefully without dirt, frost, or moisture to seal well.
- Horizontal seams are vulnerable to water penetration if tape fails. This is especially a concern at door and window tops.
- Less permeable to moisture than most building wraps, so in theory the wall may not dry out as easily.
- Not a true drainage plane, as can be created with draining building wraps. Vertical spacers or a second building wrap layer would be needed for a true drainage plane.
- If nails are overdriven, especially “shiners” missing framing, OSB is exposed and needs sealing with tape or sealant.
- More expensive materials (but savings on labor).
- On a roof, especially, I would be reluctant to trust tape to prevent leaks, so would want another roofing felt or synthetic underlayment layer.
- I would not want to screw roof steel to any OSB product.
Many builders like Zip system’s simplicity. To a large extent, its long-term performance depends on taped seam durability. If applied to a clean surface with a roller, as recommended, all indications are it will provide a long service life. This is a high-performance tape. Still, it is partly a matter of faith it will remain water tight for decades.
Alternatively, building wrap does not last forever either. It tends to get brittle and deteriorate over time. It can deteriorate rapidly if it stays wet due to trapped water — for example, if a building wrap section gets bunched up behind a trim piece as I have seen around windows, corner boards and other exterior trim.
With any waterproofing product, workmanship quality is at least as important as material. A building built well with steel siding over plastic building wrap can perform as well as one with Zip sheathing. It just a careful detailing matter — especially around doors, windows, and other joints prone to leakage.
With all of this said, yes, you could provide your own Zip sheathing and we can incorporate it in your engineer sealed plans.
3) We can provide eave sidewalls to 40 feet tall and three stories (50 feet and four stories with fire suppression sprinklers).
4) We engineer many of our buildings using poured piers and wet-set brackets. We typically provide brackets as ours have an ICC ESR Code approval and we ship them out to you far in advance of your building shell materials.
5) Our default for attached lean-to roofs would be rafters as opposed to mono-pitch trusses.