Today we’d like to revisit the “Evolution of The Pole Barn Guru and his Building Philosophy”
In my early years, tremendous quality was not necessarily the strong point. It was the ability to offer a very reasonably priced building and deliver it quickly. My buildings were pretty much the same as everyone else I competed against. Business grew and I started being able to hire employees. Jim Betonte left the steel roofing and siding industry and began a construction business which offered labor to people who wanted our building kits erected. In the mid-80’s M & W joined the National Frame Builders Association (NFBA) and started to become better educated on the “post frame” industry on the whole.
The real deal changer – in October 1985 I met Frank Woeste. Frank was an Agricultural Engineering professor at Virginia Tech and what he knew about pole buildings was staggering. In exchange for me traveling to Blacksburg, Virginia to teach one of his classes for a day, Frank gave me my first engineering design software for pole buildings and the printout of the programs in a computer program called “Basic”.
Frank motivated me to want to make better buildings and to know why it is they worked the way they did from an engineering standpoint. From
his program printout, I taught myself Basic programming and wrote more complex and varied programs than the ones which just calculated post, girt and purlin sizes.
My buildings gradually changed – steel stopped being fastened with ringshanked nails in 1982, using first galvanized, then later color matched screws. Green lumber was replaced by kiln dried lumber, much of it (especially larger sizes such as 2×6 and 2×8 with machine stress rated lumber). Utility graded skirt boards and 4×6 columns were upgraded to #2 and better. Pressure treated timbers were treated for structural in ground use, rather than “or refusal” (basically, in many cases, just coated with treating chemicals by the treatment plants).
By 1987 I had joined the American Society of Agricultural Engineers (ASAE) and the International Conference of Building Officials (ICBO). At the time, ICBO was writing the Uniform Building Code, which was adopted throughout much of the United States. The late 80’s were heady times for the ASAE as the structures committee I was a member of, was developing and putting into practice many of the standards now utilized for modern pole building structural design.
Frank Woeste and Don Bender (now a professor at Washington State University in Pullman), began holding commercial post frame design classes, which I first took as a student, and later assisted with. Often, the example buildings for the class were structures of mine.
While I owned M&W we received recognition from the State of Oregon for our donation of a building to earthquake ravaged Irkutsk, USSR. We were featured in newspapers such as the Capitol Press and magazines such as Frame Building Professional. We were also named as one of the 50 largest users of steel roofing and siding in the United States for the decade of the 1980’s. We were even featured on the morning national television program in South Korea!
In 1989, I was elected to a 3 year term on the board of directors for the National Frame Builders Association. To the best of my knowledge, I was the first board member from west of the Mississippi River.
After some 6600 building kits sold in 13 western states, Canada, Mexico and Saipan, I sold M & W Building Supply to Jim Betonte in 1990 and moved back to Spokane. My brother Mark had worked in sales for me at M & W and in 1991 he returned to Spokane as well. We formed Momb Building Systems and began constructing buildings in the Spokane area. Mark left the business in 1992 to return to school and the name was changed to Momb Steel Buildings. Business thrived and in 1993 Apex Roof Truss was begun to produce trusses and provide the lumber packages for our buildings.
Besides Washington, I became a registered contractor in Oregon, Idaho and Montana. At the height of business, we had as many as 35 crews building in six states. In one single county alone, we built over 200 buildings in a single year.
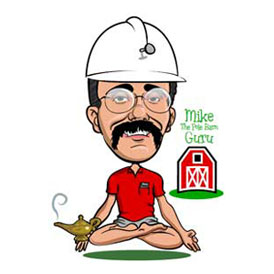
Further improvements to pole building design were made. In the early 90’s we added trims which were not regularly used along the I-5 corridor. Base trim to keep rodents out, J Channel at tops of walls, overhead door jamb trim, trims on fascias and varges with overhangs, eavelight trims with sidelight panels) all of which made for a far more attractive finished product. The first big structural change was to notch the trusses into the columns to provide direct bearing, instead of attaching them to each side of the columns. Later, we physically doubled up the trusses nailing them face-to-face, instead of blocked apart. At the same time we went to joist hanging all roof purlins between the trusses, instead of placing them lapped over the top of the truss pairs.
This now allowed for the roof panels to be predrilled before installation, which kept all screw lines straight and greatly eliminated the potential for leaks.
At an Alumax testing facility east of Los Angeles, we constructed a full scale roof to test the shear strength of steel panels. Our testing resulted in some surprises. Initially we felt the weak link would be the framing under the steel. We were totally in error and surprised at the results. Our assembly was done to match industry standards and included fastening the steel to the roof purlins using #10 x 1” screws every nine inches. As we placed horizontal loads into the roof, before ripples even appeared in the steel, the screw started to pull out of the framing. The pull out problem was solved by using 1-1/2” long screws.
The next problem was the steel began to slot beneath the screw grommets. The solution was to use larger diameter screws in the high stress areas (at the eave and ridge) and to place screws in this area on each side of each high rib, rather than along one side only. Only after all of the screw issues were solved, were we finally able to test the steel to failure. The results showed some fairly significant values. The results of this test are published in the NFBA Post Frame Building Design Manual https://bse.wisc.edu/bohnhoff/Publications/Copyrighted/NFBA_Design_Manual.pdf See Table 6.1 (assemblies 13 and 14).
After the test was completed, the Alumax design engineer, Merle Townsend designed a screw specifically to solve the weaknesses demonstrated by the test. Labeled as the “diaphragm” screw (https://lelandindustries.com/productpdfs/page%2001.pdf) this 1-1/2” part features a larger diameter shank than standard screws. A side benefit of this screw is that the larger diameter helps prevent the screw heads from twisting off during installation.
To this day, these screws remain a stable part of my building design, and have rarely (if at all) has this great improvement been equaled by any other pole building company.
Stay tuned for the final episode of “From Cradle to now…Mike the Pole Barn Guru” as he expands from four states…to fifty!