Ignorance is Bliss and Sometimes Architects are Happy
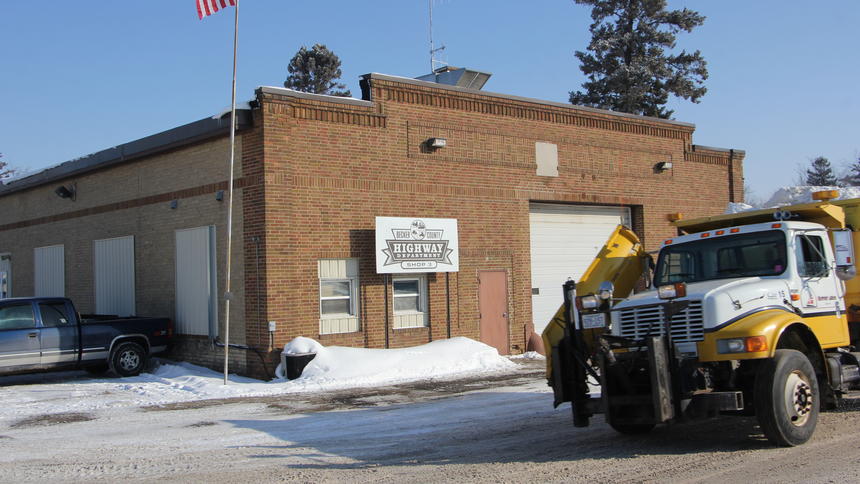
Portions of this article (in italics) are from “County explores options for new Highway building” April 29, 2019 by Nathan Bowe at www.dl-online.com
A city plow truck goes by the main shop building at the Becker County Highway Department complex in Detroit Lakes. www.dl-online.com File photo
Dear Architect friends ~ I didn’t learn much in architecture school, however one nugget was, “It is all about presentation”. Before you need to give a presentation including a possible post frame building, please discuss it with me, or at least read a few of my pertaining articles. I want you to come across as being as knowledgeable as possible.
“Hoping to save money on a new Becker County Highway Department facility, made of precast concrete and estimated to cost about $8 million, commissioners are exploring other types of buildings.
They are considering options including precast concrete, steel, and pole barn, and will tour facilities in the area made of those materials.
The firm working on the project, Oertel Architects of St. Paul, said in a report that any type of material could essentially be made to work, but a pole barn-type building would have to include steel in places to support a 5-ton crane in the maintenance area, for example.”
Post frame (pole barn) buildings can easily be designed to support a 5-ton crane: https://www.hansenpolebuildings.com/2013/07/overhead-crane/
“A less-expensive pole barn building also comes with a much shorter projected lifespan, and generally brings more problems with leaks and maintenance, unless a better grade of roof is used.”
Post frame buildings are permanent structures easily capable of generations of useful lifespan. Properly installed steel roofing will last decades without leaks or needs for maintenance.
“A pole barn is considered an agricultural type building in the industry, and is also referred to as timber frame. This is essentially like building a structure like an old-fashioned barn, with large timber columns and frames. It is typically made without a perimeter foundation. The wood frame structure is typically covered with a metal skin and the low-gable roof type is typically of metal. Its lifespan is projected at 15-30 years, depending on maintenance and other factors.”
Post frame and timber frame buildings are totally different animals. Post frame buildings have been used commercially longer than I have been in this industry (nearly 40 years). Very few buildings provided by Hansen Pole Buildings would be termed as being purely agricultural – nearly all are residential or commercial. Isolated columns embedded below frost depth preclude needs for expensive and inefficient continuous concrete foundations. (Check out foundation costs here: https://www.hansenpolebuildings.com/2011/10/buildings-why-not-stick-frame-construction/). Most typically post frame buildings have 4/12 roof slopes (rather than “low” as in all steel buildings).
Amazingly, it appears my now 15 year-old million-dollar post frame home is due to expire any time now (like Windows 7)! In reality a properly engineer designed and constructed post frame building will outlive any of us who are reading this article.
“One way to meet the highway department needs and still meet code using pole barn construction would be to build three or four separate buildings, or build one building at different heights for vehicle maintenance, vehicle washing/storage, and office space, Oertel reported.”
Post frame buildings can be easily designed with a multitude of different wall/ceiling heights.
“Pole barns tend to be less energy efficient over time.”
As post frame buildings use exact same insulations as other similar construction types, if this is true it would be applicable across all construction spectrums. Post frame lends itself well to creation of deep insulation cavities and is far easier to insulate than all steel or precast concrete.
“Structural steel works better in a public works facility, with more salt and moisture in the air than usual, since these are made of heavy steel, just like a steel bridge. It is the less substantive metal materials that are a concern. A pole barn uses thin steel gusset plates and there is not much material to last over time if corrosion is present. Metal panels commonly used in pole barn buildings are also easily marred or dented by heavy duty operations.”
In highly corrosive atmospheres, steel can be isolated from corrosion (as in galvanized steel “gusset plates” used to connect roof truss members). Any type of siding – or even precast concrete or masonry, can be damaged by careless operations. Use of strategically placed bollards (https://www.hansenpolebuildings.com/2017/05/lifesaving-bollard/) can eliminate possibilities of significant damages.
“However it’s constructed, the new public works building will need the same mechanical, plumbing and electrical systems, floor loading, earthwork and mechanical systems, Oertel said. Costs can vary, but all of that might add up to perhaps 60 percent of construction costs, with the actual building structural shell 20 to 25 percent of the total project cost. So cost savings from a cheaper type of building might not be all that commissioners might hope for, compared to the long-term drawbacks.
“More could be said about the differences between pole barn construction and a more heavy duty construction using precast concrete,” the report sums up. “It mostly comes down to a lower front-end cost with a pole barn, at the sacrifice of longevity…””
Post frame construction is going to provide a greater value, without being “cheap”. Post frame buildings will have a usable lifespan as great as any other permanent building.
And – have you ever tried to remodel a precast concrete building?